Glossy modular home websites usually focus on stunning constructions and mouth-watering interior finishes that make you fall in love with a view of your future. But, building your dream home will begin with the unglamorous task of digging a big hole for your foundations, and they have a significant role to play in your budget and project timeline.
In this article, we’ll talk about what foundations options there are for modular homes, and what you should be aware of right from the start.
What’s special about modular home foundations?
One thing that modular home construction has in common with standard on-site construction is that the foundations may account for a third of the construction cost and the highest unknown cost of the project. An industry joke is that digging foundations is like burying treasure; you dig a hole, throw your money into it, and cover it over.
Modular homes are built as a set of pieces in a factory before being transported to site, where they are assembled on top of the foundations. They have load-bearing walls, and the pieces of this giant jigsaw must be robust enough to withstand the process of transportation to site. These key differences to standard on-site construction mean that the requirements for the foundations are also different.
Foundations are intrinsically different to the rest of the modular home in that the home is built in a factory and can be placed anywhere that is considered suitable. In contrast, foundations are absolutely specific to their location, based on the soil and topography on site.
How do I know which foundations to use?
Almost all modular home manufacturers offer a foundation design service, and some install the foundations. At the very least, they will tell you what you need to have in place in terms of dimensions and load capacity. They may also give you a few options with costings.
Different manufacturers may favour a particular type of foundations. It might be that they work well with their house assembly, have developed a partnership with a foundations specialist, or use materials and processes that enable them to deliver for the most competitive price or the least environmental impact.
When you look at different modular homes, always ask about foundations, as they will greatly affect the overall cost of your house, the environmental impact, and the time it takes to build. You may already know whether you want a manufacturer to take care of the foundations, or you might be keen to manage or even install the foundations yourself to reduce costs. Either way, it’s worth understanding the common foundations types, so you know what architects and engineers are talking about.
What options or types of foundations can you consider for a modular home?
Raft foundations
A major benefit of modular homes is that, because the walls are load-bearing and robust, raft foundations are appropriate in many cases. This involves little or even no digging, and then laying a slab which can be as little as 100mm-150m thick, laid to the dimensions specified by the modular home manufacturer.
The raft is made by pouring concrete, limecrete or hempcrete into a mold which can be formed by low brickwork or by digging a shallow and level hole. In most cases, a dampproof membrane would be laid into the hole, followed by insulation to reduce heat loss from the house into the ground, then sand, and finally, the wet mix that forms the slab, which needs to be worked to ensure it is level when complete. Steel or other reinforcement may be required, depending on the engineer’s foundations design.
The amount of insulation is often specified by the architect (either independent or manufacturer’s architect) in order that the house conforms to building regulations regarding heat loss. They will also specify the correct mix for the slab, and the correct depth in order to have the required strength. An eco-friendly insulation option here is recycled foam glass.
Slab foundations do not have any space underneath either for a basement, storage, or installing services, which all need to be laid in place before the wet mix is poured into the mold.
Another crucial consideration is to ensure that the slab or raft will not subside with the weight of the house. Soil samples can be analysed from different parts of the site, and the history of the site and the areas considered so that an engineer can have reasonable confidence the house will not subside over the years. For example, there may be careful consideration in an area of history open cast mining or other features that may make the ground prone to uneven density.
Strip foundations
Strip foundations are standard for all sorts of house construction, and they can be used for modular homes too. Under the position of load-bearing walls, which for modular homes are the exterior walls or even all walls, a trench is dug out of around 1 metre deep and half a metre wide. These trenches are then filled with concrete, forming ‘strips’.
Strip foundations are deeper, more stable, and use more material than slab foundations. They are, therefore, more expensive but often preferred where there is soft ground. Once the strip foundations are dug and filled with concrete, you can lay a dampproof membrane, insulation, and a slab.
As with the slab, you can choose insulation material, working with your architect to ensure that you install sufficient depth to be compliant with building regulations and achieve the build quality that you want.
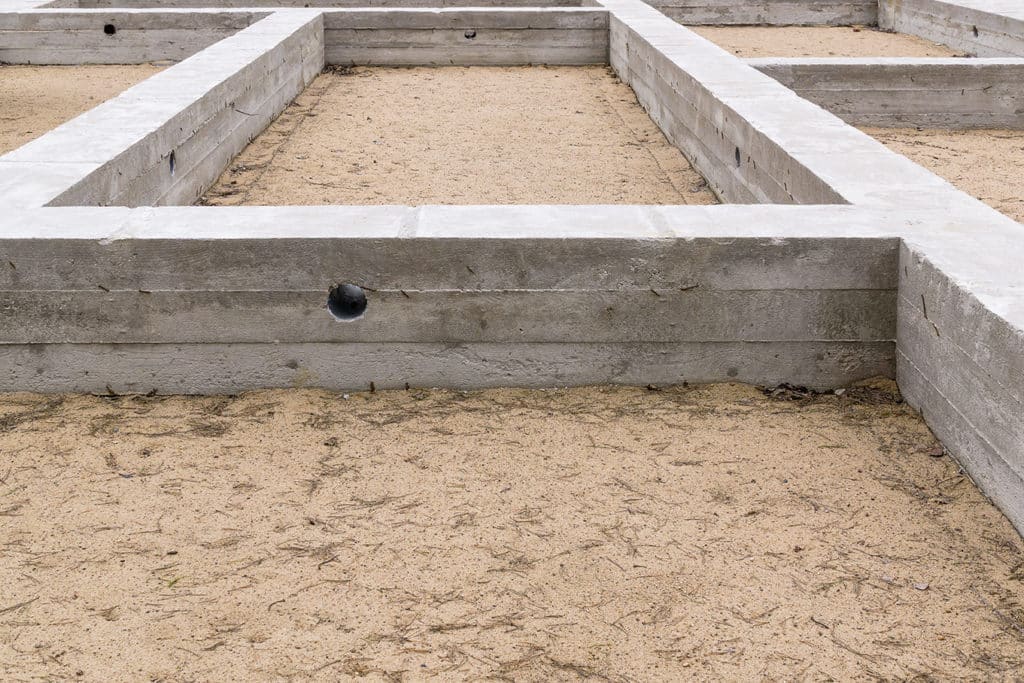
Pad foundations
These are like strip foundations, but they are individual pads placed under load-bearing points. These are rarely used with modular homes because walls a load-bearing rather than specific points. However, they may be used on sites with a steep inclination to avoid digging deep into the hill and to ensure that a flying edge is adequately supported. As with any modular home foundation, a structural level platform would be installed above the foundations to support those load-bearing walls.
Deep foundations
Steel piles or reinforced concrete piles may be necessary where the top layers of soil do not provide adequate support for the house.

Basement foundations
If you want storage space, a crawl space under the house, or a basement, then ask your architect and engineer to provide design and specifications, respectively. This option is the most expensive as it requires deeper excavations and more reinforced concrete to secure the ground or build up to the floor level. At floor level, the slab is installed for the modular home to be assembled as with any other foundations.
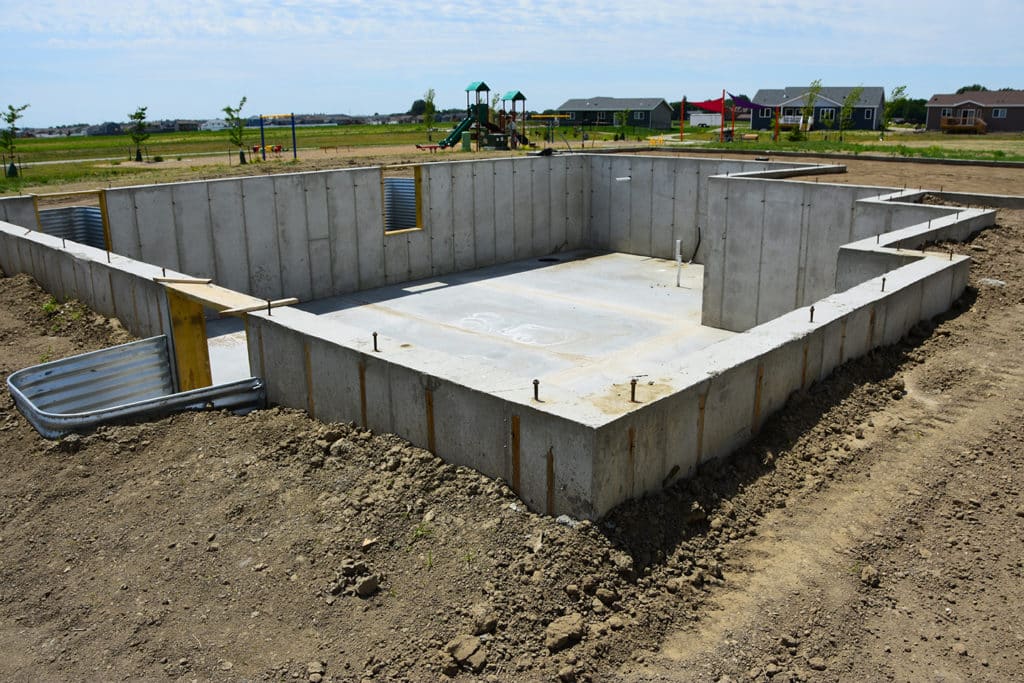
How much do foundations cost?
Foundations may cost up to a third of your construction budget, as a rule of thumb, because of the cost of excavation, with the risk of difficult ground and the sheer quantity of material and labor that goes into preparing and pouring foundations to specification.
The cost varies massively depending on the ground’s type and inclination, the foundations’ specification, and the materials selected. Foundations are labour-intensive and can take much longer than expected if difficult ground conditions are encountered, so the costs of local labour and availability are another significant variable.
In the UK checkatrade.com give an estimated average cost per square metre of 260 Euros. So, as a very basic starting point, take the square meterage of the ground floor of the modular home that you are considering, and then multiply it by 260 Euros. Ideally, you then add 20% to allow for variability before you include it in your budget right from the start of your journey.
Conclusion
Consider foundations from early on to optimise your build budget and performance. They may not be as exciting as the designs of beautiful modular houses, but their impact on your budget and timescale may affect your financial capacity to enjoy interior design choices later on. In every opening conversation with a modular home manufacturer, ask what they offer regarding foundations.
A local groundworks company is best placed to excavate because they are used to this terrain, soil type, whether the home manufacturer hires them, or you do.
A local builder or you should be able to follow the architect’s specification to install foundations correctly, though it is essential that your local building control inspect the site at the required points, for example, inspecting the trench before you pour concrete into it. It’s essential that you get all details correct to specification, including the concrete mix, the laying of the dampproof membrane with edge detailing, the positioning of pipes and services, and the careful installation of insulation to avoid cold spots on your new floor.
You might save money by doing it yourself or contracting someone local. But, if the home manufacturer is not satisfied that the slab is to their specifications or not sufficiently level, they may not be willing to assemble the house until it is corrected. This is reasonable as it could affect the stability of the house or the alignment of construction modules.